The Impact of Digital Twins and IoT on the Shell & Tube Heat Exchanger Market: Revolutionizing Monitoring and Performance
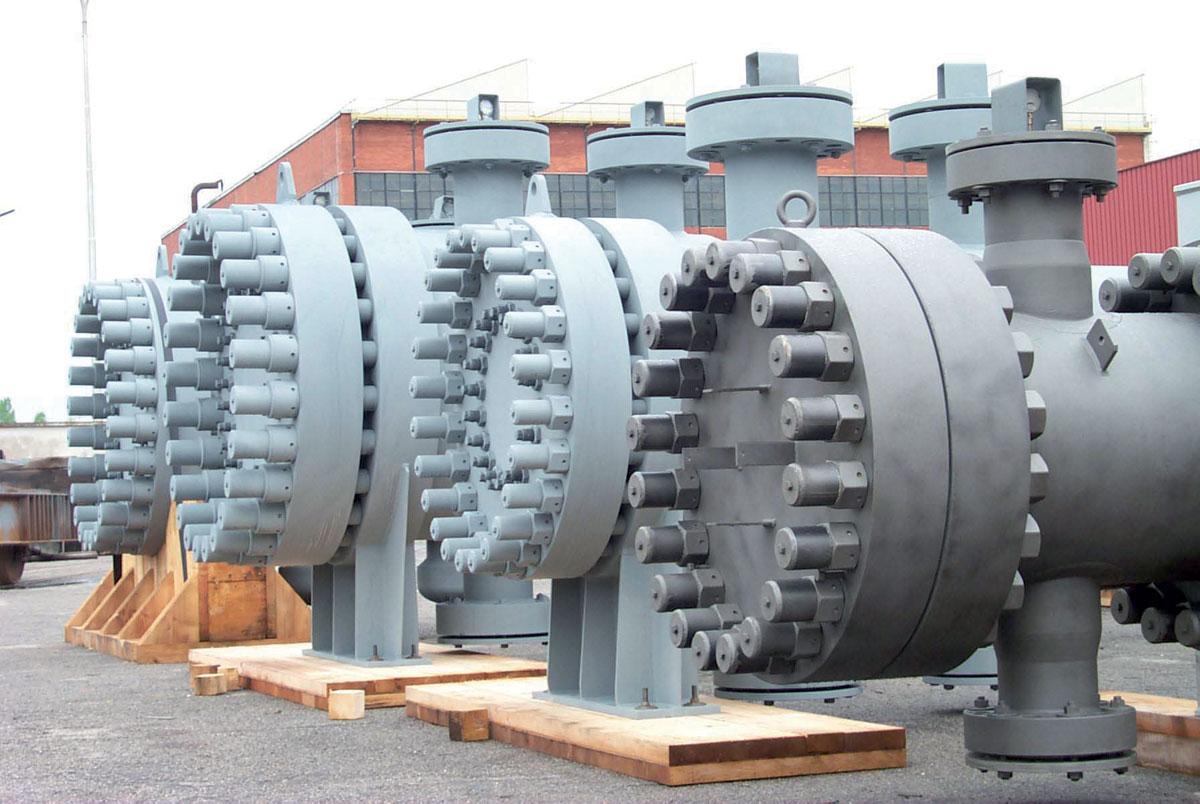
Introduction
The Shell & Tube Heat Exchanger (STHE) Market has seen significant advancements with the integration of Digital Twin technology and the Internet of Things (IoT). These innovations have not only improved the operational efficiency of heat exchangers but have also paved the way for predictive maintenance, performance optimization, and a reduction in downtime. This article explores the impact of these cutting-edge technologies on the market and how they are revolutionizing the monitoring and performance of Shell & Tube Heat Exchangers.
Understanding Shell & Tube Heat Exchangers
Shell & Tube Heat Exchangers (STHEs) are vital components used in a wide range of industries, including oil and gas, chemical processing, HVAC, and power generation. They consist of a series of tubes, one carrying the hot fluid and the other carrying the cold fluid, allowing heat transfer between the two. These exchangers are renowned for their high efficiency and versatility, making them indispensable in various industrial applications.
Given their critical role in these industries, ensuring the optimal performance and reliability of STHEs is paramount. This is where innovations like Digital Twins and IoT are making an enormous difference.
The Role of Digital Twin Technology in Shell & Tube Heat Exchangers
Digital Twin technology refers to a virtual replica of a physical object, system, or process, used for simulation and real-time monitoring. For Shell & Tube Heat Exchangers, a Digital Twin enables the creation of an accurate virtual model that mimics the physical properties and behavior of the heat exchanger.
With the help of sensors and IoT integration, the Digital Twin can replicate the heat exchanger's physical environment, offering valuable insights into its performance. By continually receiving data from the actual heat exchanger, the Digital Twin allows operators to analyze the behavior of the system in real-time, identify potential issues, and simulate various operational scenarios to optimize performance.
Predictive Maintenance with Digital Twin Technology
One of the most significant advantages of incorporating Digital Twin technology into Shell & Tube Heat Exchangers is predictive maintenance. Traditional maintenance schedules are often based on fixed intervals or reactive measures, which can lead to unexpected breakdowns and costly repairs. However, with the Digital Twin, maintenance can be more data-driven and predictive.
By continuously monitoring the heat exchanger's virtual twin, operators can track key performance indicators (KPIs), such as temperature, pressure, flow rate, and heat transfer efficiency. This data allows for the detection of anomalies or potential failures before they escalate into major issues. For instance, the system might predict a drop in heat transfer efficiency due to fouling or corrosion, allowing operators to take proactive measures, such as cleaning or part replacement, before the exchanger fails.
This predictive approach not only reduces downtime but also extends the lifespan of the heat exchangers, saving costs in the long run.
The Role of IoT in Enhancing Heat Exchanger Performance
The Internet of Things (IoT) has become an essential part of modern industrial operations. For Shell & Tube Heat Exchangers, IoT-enabled sensors and devices help collect real-time data on various performance parameters, such as temperature, pressure, fluid flow, and vibration levels. This data is transmitted to cloud-based platforms, where it can be processed, analyzed, and used to make informed decisions.
IoT connectivity allows for the continuous monitoring of heat exchanger performance, making it easier to detect problems early on. For example, if a temperature sensor detects an abnormal rise in temperature, operators can intervene before the issue leads to catastrophic failure. IoT can also be integrated with advanced analytics to predict the future state of the equipment based on historical data, operational patterns, and environmental factors.
Integrating Digital Twins and IoT for Maximum Impact
The combination of Digital Twin technology and IoT has a synergistic effect on the Shell & Tube Heat Exchanger market. While IoT enables the collection of real-time data, the Digital Twin creates a virtual environment for analyzing and simulating the system's behavior.
This integration enables operators to monitor the actual performance of heat exchangers and test various “what-if” scenarios virtually, enhancing the decision-making process. For instance, if operators notice increased pressure in a specific section of the heat exchanger, they can simulate the impact of cleaning or adjusting flow rates on the virtual model before taking action on the physical system.
Moreover, the integration of these technologies helps in optimizing energy consumption, reducing waste, and improving overall system efficiency. By continuously optimizing the performance of heat exchangers, industries can lower their operational costs, increase productivity, and minimize their environmental impact.
Advancements in Real-Time Monitoring and Performance Optimization
Real-time monitoring is one of the most powerful benefits of combining Digital Twins and IoT for Shell & Tube Heat Exchangers. With constant feedback loops from IoT sensors, operators can observe real-time data from various points in the heat exchanger system, from inlet temperatures to pressure differentials. The Digital Twin utilizes this data to reflect current operational conditions and simulate the performance of the entire system.
For instance, if a heat exchanger is experiencing excessive pressure drop, the system can instantly analyze the cause, whether it's due to fouling, blockage, or other operational inefficiencies. This immediate identification enables prompt corrective actions, thus preventing further degradation in performance and minimizing downtime.
Reducing Operational Costs Through Smart Energy Management
Energy efficiency is a major concern in industrial applications, and Shell & Tube Heat Exchangers are no exception. IoT sensors monitor energy consumption in real time, helping operators identify patterns that might lead to excessive energy use. Combined with the Digital Twin's predictive analytics capabilities, it is possible to adjust operational parameters and optimize energy consumption.
For example, if the heat exchanger is consuming more energy than usual, the Digital Twin can simulate alternative operational configurations to find the most energy-efficient one. Additionally, IoT sensors help monitor external factors such as ambient temperature or humidity, which may influence the heat exchanger's performance. This granular level of control helps reduce energy costs and improve the sustainability of operations.
Enhancing Design and Innovation through Simulation and Testing
The ability to test new designs and configurations through simulation is another valuable benefit of Digital Twin technology. When designing a new Shell & Tube Heat Exchanger or upgrading an existing one, engineers can leverage the Digital Twin model to simulate different design parameters, such as tube sizes, materials, and configurations.
By running simulations, engineers can evaluate how these changes might impact heat transfer efficiency, pressure drop, and energy consumption. These simulations help optimize the design before physical manufacturing begins, leading to faster product development cycles and reduced risk of costly design flaws.
Conclusion
The Shell & Tube Heat Exchanger market is undergoing a transformation, driven by the integration of Digital Twin technology and the Internet of Things. These innovations have revolutionized the way heat exchangers are monitored, maintained, and optimized for performance. By enabling predictive maintenance, real-time monitoring, and energy optimization, Digital Twins and IoT are enhancing the efficiency, reliability, and lifespan of Shell & Tube Heat Exchangers.
As industries continue to embrace these technologies, the future of Shell & Tube Heat Exchangers looks promising, with further advancements expected in energy efficiency, cost savings, and system performance. The continued development and integration of IoT and Digital Twin technologies will play a crucial role in shaping the next generation of heat exchangers, ushering in a new era of intelligent, data-driven operations.
- Art
- Causes
- Crafts
- Dance
- Drinks
- Film
- Fitness
- Food
- Игры
- Gardening
- Health
- Главная
- Literature
- Music
- Networking
- Другое
- Party
- Religion
- Shopping
- Sports
- Theater
- Wellness
- IT, Cloud, Software and Technology