How Kawasaki and Daihen are Shaping the Future of Wafer Handling Robotics
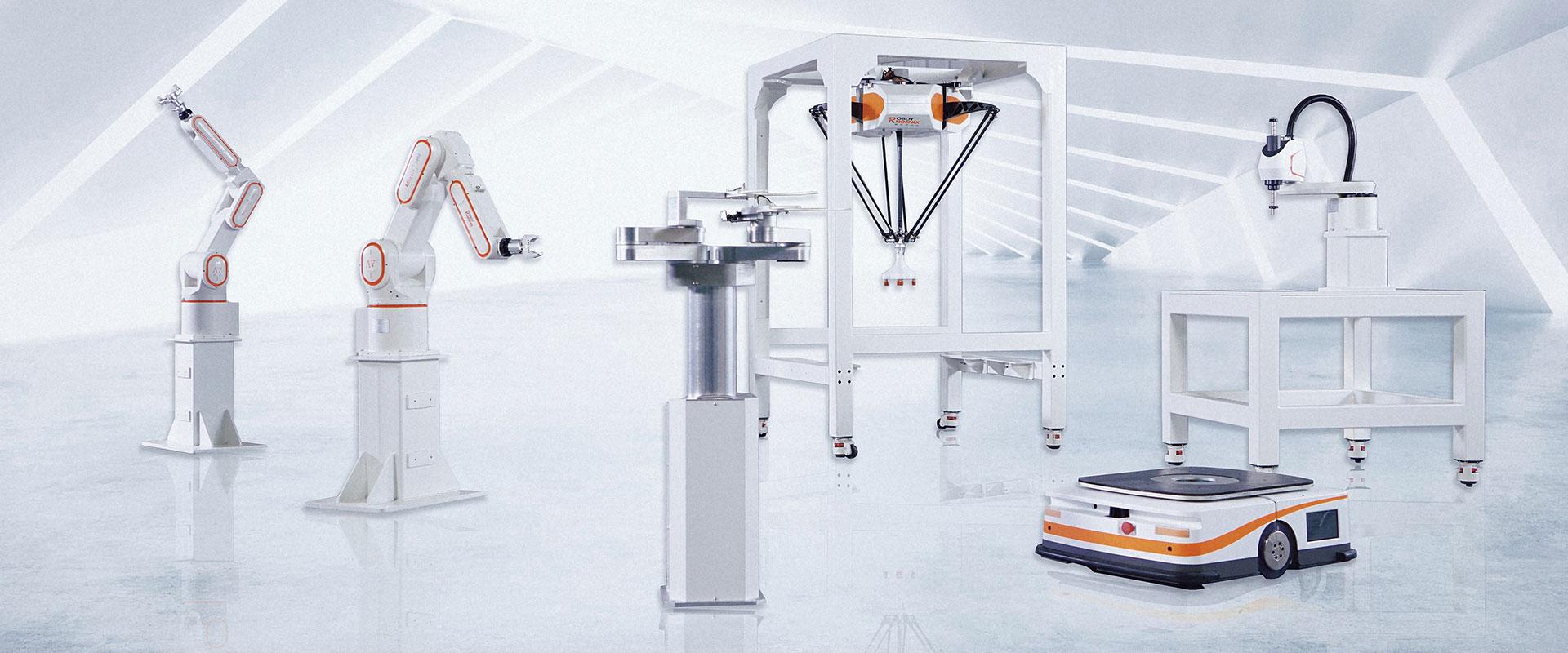
Introduction:
The semiconductor industry is undergoing a profound transformation, driven by innovations in technology that are paving the way for faster, more efficient, and more sustainable manufacturing processes. Among these innovations, wafer handling robotics are emerging as a key enabler for enhancing the precision, speed, and cost-effectiveness of semiconductor production. At the forefront of this revolution are two robotics giants: Kawasaki Robotics and Daihen Corporation. Both companies are playing pivotal roles in shaping the future of wafer handling, particularly by tackling the unique challenges posed by the rise of 3D wafer handling.
In this article, we will explore how Kawasaki and Daihen are addressing the challenges of 3D wafer handling and how their advanced robotic technologies are improving the efficiency and quality of semiconductor manufacturing. From high-precision movements to integration with cutting-edge automation systems, we will delve into the key factors driving the success of these innovations in wafer handling robotics.
Understanding 3D Wafer Handling in Semiconductor Manufacturing
3D wafer handling is a next-generation approach to semiconductor manufacturing that aims to increase the density and performance of chips. Unlike traditional 2D wafer manufacturing, where integrated circuits are etched and layered in a single plane, 3D wafer processing involves stacking multiple layers of wafers, sometimes with intricate wiring connections between them. This enables the production of more powerful and compact semiconductor devices.
However, 3D wafer handling presents several technical challenges. These include:
-
Increased fragility: Stacked wafers are often thinner and more fragile than single wafers, making handling more delicate and prone to breakage.
-
Precision requirements: 3D wafers need to be aligned and stacked with extreme precision to ensure that the layers are properly bonded and electrically connected.
-
Cleanroom conditions: The wafer handling process must occur in controlled environments to prevent contamination, as even the smallest particle can damage the wafer or interfere with the manufacturing process.
-
Complexity in automation: Handling, aligning, and moving 3D wafers require robotic systems to integrate with other systems in the production line and handle wafers in multiple orientations.
With these challenges in mind, both Kawasaki Robotics and Daihen Corporation have developed cutting-edge robotic solutions to address these complexities and take 3D wafer handling to new heights of efficiency and precision.
Kawasaki Robotics: Leading the Way in 3D Wafer Handling
Kawasaki Robotics has long been recognized for its contributions to automation and robotics, particularly in industries such as semiconductor manufacturing. The company’s expertise in precision robotics and advanced automation systems has made it a leader in the development of solutions for 3D wafer handling.
1. High-Precision Robotics for Fragile 3D Wafers
Handling 3D wafers with precision is a complex task. Kawasaki Robotics has risen to this challenge with its state-of-the-art robotic arms and vision systems. These systems are specifically designed to manipulate delicate wafers without causing damage, ensuring that 3D wafers are transported, stacked, and aligned with exceptional precision.
Kawasaki's robotic arms, such as the RS series, are known for their micrometer-level accuracy. This is critical for 3D wafer handling, as even the slightest misalignment can lead to defects in the semiconductor devices. By utilizing advanced sensors and vision systems, Kawasaki's robots are capable of detecting minute shifts in wafer positioning, adjusting their movements accordingly, and ensuring that the wafers are handled properly throughout the entire process.
2. Automated Alignment and Stacking Systems
One of the key innovations that Kawasaki has introduced is the automated alignment and stacking system for 3D wafers. In 3D wafer manufacturing, it is essential that each wafer layer is aligned precisely to ensure proper electrical connections between the layers. This alignment process is highly complex and requires a level of precision that is difficult to achieve manually.
Kawasaki’s robotic systems are equipped with cutting-edge vision-based alignment technology that enables them to detect the position and orientation of each wafer with incredible accuracy. The robots can then perform automated stacking, placing each wafer layer in perfect alignment with the previous one. This not only reduces the risk of human error but also accelerates the production process.
3. Advanced Integration with Production Lines
To address the challenges of integrating 3D wafer handling with the overall semiconductor production process, Kawasaki Robotics has focused on creating intelligent robotic systems that can seamlessly communicate with other automation equipment. This integration ensures that the robotic systems can work in harmony with wafer processing chambers, cleanrooms, and other machinery in the production line.
The integration of Kawasaki's robotic systems into the overall automation framework also allows for real-time monitoring and data collection. This data can be used to optimize the performance of the entire production line and predict maintenance needs, further improving the efficiency of the manufacturing process.
Daihen Corporation: Advancing the Art of 3D Wafer Handling
Daihen Corporation is another robotics leader that is making significant contributions to the field of 3D wafer handling. With a focus on advanced robotics and intelligent automation, Daihen is helping semiconductor manufacturers overcome the challenges associated with the increasing complexity of 3D wafer production.
1. Sophisticated Handling Mechanisms for 3D Wafers
Daihen’s robots are designed to handle the complexities of 3D wafer stacking by using sophisticated gripper systems. These grippers are capable of securely holding fragile 3D wafers while they are being moved between different stages of production. The grippers are equipped with sensors that can detect the wafer’s orientation, ensuring that it is held correctly throughout the entire handling process.
Daihen’s robots are also built to handle wafers of varying sizes and thicknesses, which is essential in 3D wafer production, where the dimensions of wafers can vary based on the design and application of the semiconductor. Daihen’s robotic systems are highly adaptable, enabling manufacturers to customize the handling process for different wafer types without compromising performance.
2. Automation and Predictive Maintenance
Daihen’s commitment to automation extends beyond the physical handling of wafers. The company’s robotic systems are integrated with advanced machine learning algorithms that enable them to continuously improve their handling processes. By analyzing real-time data, Daihen’s robots can predict potential issues before they occur, ensuring that any maintenance needs are addressed proactively.
Predictive maintenance is particularly important in 3D wafer handling, where any downtime can significantly affect production schedules. Daihen’s robots help manufacturers minimize downtime and ensure that their production lines remain up and running smoothly, thus increasing overall efficiency.
3. Cleanroom Compatibility
3D wafer handling must take place in ultra-clean environments to avoid contamination, which could compromise the integrity of the wafers and the resulting semiconductor devices. Daihen’s robots are engineered to operate in cleanroom conditions, maintaining a high level of cleanliness while handling delicate wafers. This ensures that wafers are moved without introducing contaminants, which is crucial in the production of high-performance semiconductors.
Daihen’s robots are equipped with antistatic features and cleanroom-compatible materials, making them ideal for the rigorous demands of semiconductor manufacturing environments.
How Kawasaki and Daihen Are Tackling the Challenges of 3D Wafer Handling
The challenges of 3D wafer handling require highly specialized robotic systems that can offer extreme precision, adaptability, and reliability. Both Kawasaki Robotics and Daihen Corporation have risen to meet these demands by developing advanced robotic technologies that address the key pain points of 3D wafer production.
1. Precision and Accuracy
Both companies focus heavily on precision handling, a critical requirement for 3D wafer stacking. By using advanced vision systems, sensors, and high-precision robotic arms, Kawasaki and Daihen ensure that wafers are moved with the utmost care and accuracy, eliminating the risk of defects that can occur from misalignment or mishandling.
2. Energy-Efficiency and Sustainability
In addition to precision, energy efficiency is another focus for Kawasaki and Daihen. Their robotic systems are designed to minimize energy consumption, which is important in an industry known for its high energy requirements. By optimizing robotic movements and utilizing intelligent energy management, both companies help reduce the overall energy footprint of semiconductor manufacturing.
3. Integration with Advanced Automation
Both Kawasaki and Daihen have taken steps to ensure that their robots integrate seamlessly with other automation systems in semiconductor manufacturing. This integration allows for optimized workflows, real-time data analysis, and predictive maintenance, all of which contribute to a more efficient and sustainable production process.
4. Cleanroom Compatibility
Lastly, both companies have developed robotic systems that are compatible with cleanroom environments, ensuring that 3D wafers are handled without introducing contamination. This is particularly important in the semiconductor industry, where even the smallest particle of dust can ruin a wafer.
Conclusion
The rise of 3D wafer handling is revolutionizing the semiconductor industry, and companies like Kawasaki Robotics and Daihen Corporation are leading the charge with their advanced robotic solutions. By tackling the challenges of precision, fragility, automation, and cleanroom compatibility, these companies are enabling semiconductor manufacturers to produce high-performance chips with greater efficiency and sustainability.
As the demand for semiconductors continues to grow, innovations in 3D wafer handling robotics will play an increasingly vital role in meeting the challenges of the future. With ongoing advancements in automation, energy efficiency, and precision, the future of wafer handling looks brighter than ever.
- Art
- Causes
- Crafts
- Dance
- Drinks
- Film
- Fitness
- Food
- Jeux
- Gardening
- Health
- Domicile
- Literature
- Music
- Networking
- Autre
- Party
- Religion
- Shopping
- Sports
- Theater
- Wellness
- IT, Cloud, Software and Technology