Graph Technologies Market: Revolutionizing Predictive Maintenance in Industrial IoT
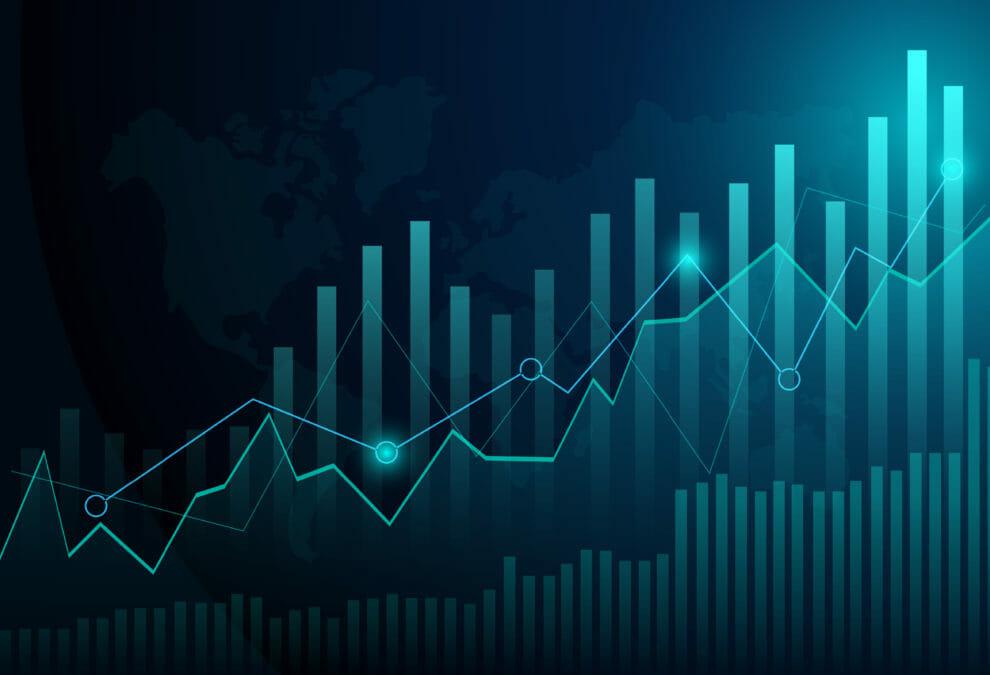
Introduction:
In recent years, the Graph Technologies Market has experienced significant growth, driven by the increasing need for advanced data management and analysis tools across various industries. As industries evolve, the need for more efficient and intelligent systems has led to the integration of Graph Technologies with cutting-edge applications such as Predictive Maintenance in Industrial Internet of Things (IIoT). This integration has emerged as a powerful way to improve operational efficiency, reduce downtime, and enhance productivity in industrial environments. In this article, we will explore the role of graph technologies in predictive maintenance within IIoT and how this combination is shaping the future of industrial operations.
Understanding Graph Technologies in the Industrial Context
Graph technologies refer to data models and management systems that represent and process data through a graph structure, which includes nodes, edges, and properties. These technologies enable businesses to better represent complex relationships and patterns within their data, which is especially valuable in scenarios where data points are interrelated.
In the context of industrial applications, graph technologies are used to model the intricate connections between different elements of an operation—such as machinery, components, sensors, and maintenance events. The ability to easily query and analyze these relationships allows for more insightful and dynamic decision-making, which is essential for industries like manufacturing, energy, transportation, and more.
With the integration of IoT sensors and real-time data collection systems, industrial operations are generating massive volumes of data. Graph technologies help organize and structure this data in a way that provides valuable insights into the operational health of machinery and equipment. This ability is particularly important in predictive maintenance, where organizations aim to anticipate and prevent equipment failure before it happens.
The Role of Predictive Maintenance in Industrial IoT
Predictive maintenance refers to the practice of using data-driven insights to predict and prevent equipment failures before they occur. Traditional maintenance strategies, such as reactive and preventive maintenance, often result in unnecessary downtime and costly repairs. Reactive maintenance occurs after a failure, while preventive maintenance is based on fixed schedules that may not accurately account for real-world wear and tear on equipment.
Predictive maintenance, on the other hand, uses real-time data collected from sensors and devices embedded within machinery to monitor the condition of equipment continuously. By analyzing this data, companies can identify patterns and trends that indicate potential failures, allowing for timely intervention. This proactive approach helps reduce operational disruptions, extend the lifespan of assets, and reduce maintenance costs.
The integration of IoT devices and sensors has made predictive maintenance more accessible, providing a wealth of data to monitor machine health. However, to unlock the full potential of this data, companies need advanced technologies that can analyze and interpret the complex relationships between various data points. This is where graph technologies come in.
How Graph Technologies Power Predictive Maintenance
Graph technologies have emerged as a key enabler for predictive maintenance in the context of Industrial IoT. Here's how they play a crucial role:
1. Enhanced Data Representation and Analysis
In industrial IoT environments, there are often many different types of data sources—each producing vast amounts of data. These sources could include sensor data (temperature, vibration, pressure), maintenance logs, equipment specifications, and more. Graph databases excel at integrating and storing heterogeneous data from multiple sources, allowing all the data to be represented in a unified, interconnected structure.
For example, graph technologies can map out the relationships between machines, components, sensors, and maintenance records. By visualizing these relationships, engineers can quickly identify patterns of failure across various parts of the system and trace the underlying causes of issues. This is particularly useful for identifying hidden correlations between different equipment components that might not be obvious using traditional relational database models.
2. Real-Time Monitoring and Fault Detection
In industrial IoT applications, data is continuously generated by various sensors embedded in machinery. Graph databases are optimized for managing this dynamic and real-time data. The ability to perform quick and efficient queries on this real-time data helps operators monitor the health of equipment continuously.
For example, by analyzing the connections between sensor data (such as vibration readings) and failure events (such as breakdowns), graph technologies can help detect early signs of impending failure. Predictive models built using graph databases can analyze historical data alongside current sensor data to forecast future equipment issues, triggering alerts when certain thresholds are reached.
Graph databases are also excellent for creating predictive models that account for interdependencies between components and systems. For instance, if a specific component’s failure pattern is linked to a larger system failure, the graph model can indicate how failure in one area could cascade throughout the system. This helps organizations make more accurate predictions about when a failure is likely to occur and the scope of its impact.
3. Improved Fault Diagnosis and Root Cause Analysis
One of the key benefits of graph technologies in predictive maintenance is their ability to support efficient root cause analysis (RCA). When a failure occurs, identifying the root cause is often a complex and time-consuming process. Traditional approaches typically involve looking at a variety of data sources individually, which can be inefficient.
In contrast, graph databases allow operators to trace back through the entire network of connected data, from sensors to machines to maintenance history. By visualizing these relationships, engineers can more easily identify the true cause of a failure. For example, if a pump failure is linked to a vibration issue, graph technologies can help track this connection back to a specific mechanical issue or part failure. This accelerates the diagnosis process and helps to prevent similar failures from occurring in the future.
4. Predictive Analytics with AI and Machine Learning
As graph technologies continue to evolve, they are increasingly being integrated with artificial intelligence (AI) and machine learning (ML) algorithms. These technologies can automatically analyze large datasets, identify trends, and make predictions based on patterns within the data.
By applying AI and ML techniques to data stored in a graph database, companies can develop more sophisticated predictive models. For example, algorithms can identify correlations between different types of sensor data and maintenance history that humans may not easily notice. These models can predict when an equipment failure is most likely to occur, allowing for better planning and scheduling of maintenance.
Graph technologies are also being used to continuously refine and improve predictive models as new data is collected. By analyzing past failures and maintenance activities, AI models can be trained to become more accurate over time, helping organizations make better predictions and optimize their maintenance schedules.
5. Optimizing Spare Parts Management
An often-overlooked aspect of predictive maintenance is spare parts management. Efficiently managing spare parts inventory is crucial for minimizing downtime during maintenance and repairs. Graph databases can help optimize spare parts management by mapping out the relationships between equipment, components, and maintenance activities.
For instance, graph models can track which components fail most frequently and how long it typically takes for parts to be replaced. This information helps organizations maintain an optimal inventory of spare parts, ensuring they have the necessary components on hand when an issue is detected. This can prevent delays in repairs and minimize machine downtime.
The Future of Graph Technologies in Predictive Maintenance
As the Industrial IoT market continues to expand, the role of graph technologies in predictive maintenance is set to grow. By offering advanced capabilities for real-time monitoring, predictive analytics, and root cause analysis, graph databases are becoming essential tools for manufacturers, energy producers, and other industrial enterprises.
Looking ahead, there are several emerging trends that are likely to drive further innovation in this space:
-
Integration with 5G: The roll-out of 5G networks will allow for faster and more reliable real-time data transmission in industrial environments. This will enable more efficient predictive maintenance solutions powered by graph databases.
-
Cloud-Based Graph Databases: As organizations move toward cloud computing, graph databases are increasingly being hosted on cloud platforms. Cloud-based solutions offer scalability, flexibility, and reduced IT overhead, making them an attractive option for predictive maintenance.
-
Edge Computing: With the growing demand for real-time analysis, edge computing is emerging as a key trend. By processing data closer to where it is generated (i.e., at the edge of the network), organizations can make quicker decisions and reduce latency in predictive maintenance applications.
-
Blockchain Integration: Blockchain technology may also play a role in predictive maintenance by providing secure and transparent tracking of maintenance histories and parts replacements.
Conclusion
The integration of Graph Technologies with Predictive Maintenance in Industrial IoT is transforming the way companies manage their operations. By enabling more efficient fault detection, root cause analysis, and predictive analytics, graph databases are empowering organizations to optimize equipment performance and reduce operational costs.
As industries continue to embrace the benefits of real-time data analysis and advanced predictive models, the role of graph technologies in predictive maintenance will only continue to grow. With emerging technologies like AI, cloud computing, and edge computing, the future of industrial operations looks poised for further innovation and optimization through the power of graph technologies.
- Art
- Causes
- Crafts
- Dance
- Drinks
- Film
- Fitness
- Food
- Jocuri
- Gardening
- Health
- Home
- Literature
- Music
- Networking
- Alte
- Party
- Religion
- Shopping
- Sports
- Theater
- Wellness
- IT, Cloud, Software and Technology