Silyl Modified Polymer (SMP) Manufacturing Plant Project Report 2025: Manufacturing Plant Setup and Operations
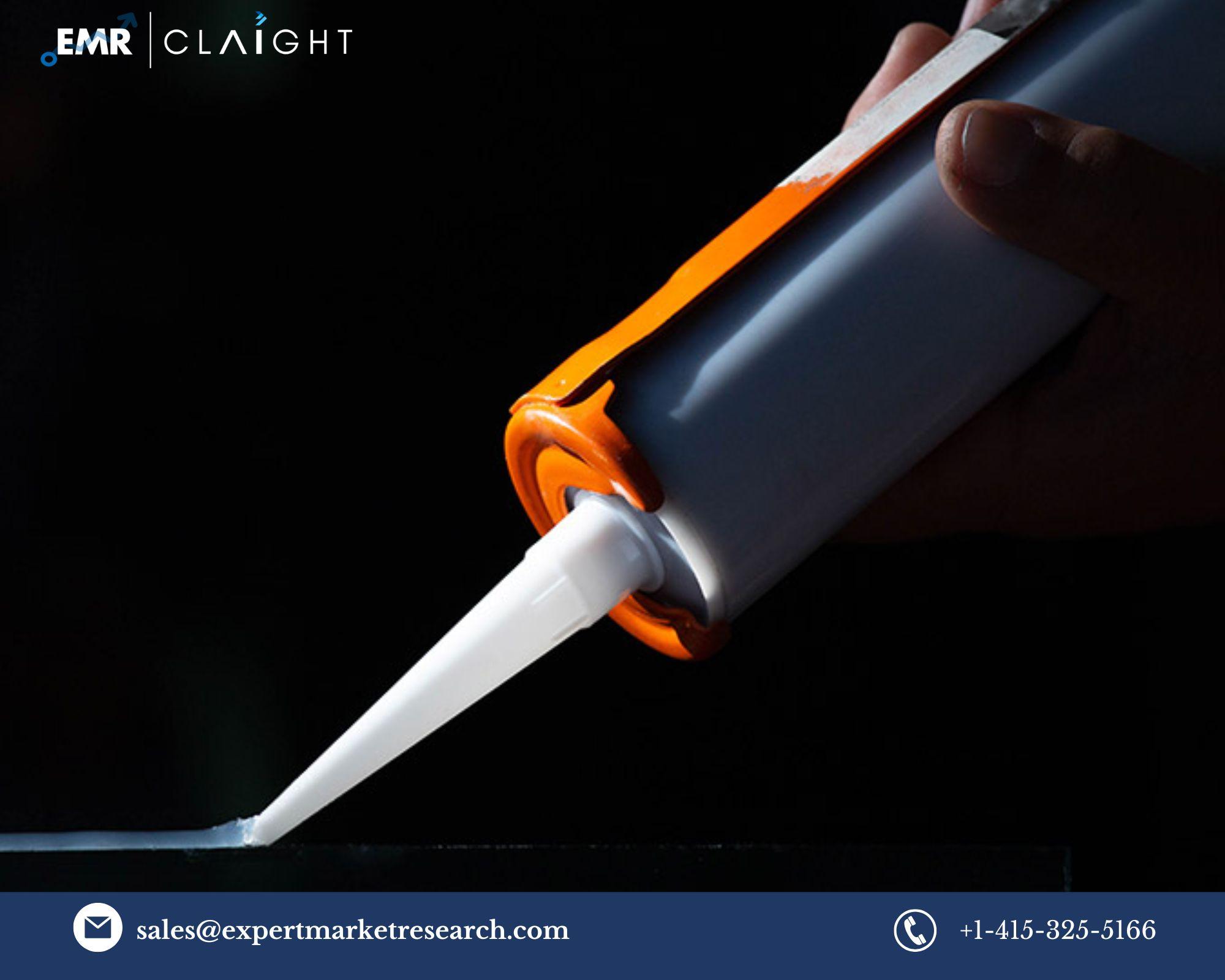
Introduction
The Silyl Modified Polymer (SMP) Manufacturing Plant Project Report serves as a comprehensive guide for establishing a facility dedicated to the production of silyl-modified polymers. Silyl-modified polymers have become increasingly popular in various industries due to their versatility and superior performance characteristics. These polymers combine the best properties of both silicones and organic polymers, resulting in high-quality, durable materials. SMPs are widely used in sealants, adhesives, coatings, and construction materials, among other applications.
The rise in demand for environmentally friendly, high-performance products in construction, automotive, and electronics sectors has made SMPs a sought-after solution for manufacturers. This report outlines the essential steps involved in establishing an SMP manufacturing plant, including market analysis, technical specifications, financial considerations, and project management.
Understanding Silyl Modified Polymers (SMPs)
Before diving into the manufacturing plant project details, it is important to have a solid understanding of what silyl-modified polymers are and why they are highly valued in the industrial sector. SMPs are a class of polymers that are modified with silyl groups (functional groups containing silicon and oxygen) at the polymer chain ends. These modifications offer improved performance in terms of moisture resistance, adhesion, and flexibility.
The molecular structure of SMPs allows them to form stronger bonds with substrates like metals, plastics, and glass, making them ideal for use in a range of industries. They are also known for their low volatility, which helps reduce environmental impact. Their unique properties allow SMPs to serve as alternatives to conventional silicones and polyurethanes in several demanding applications.
Market Demand and Applications of SMPs
Growing Demand in the Construction Industry
One of the major drivers of SMP demand is the construction industry. SMPs are widely used in sealants and adhesives that offer long-lasting performance in building materials. These polymers are particularly effective in weatherproofing, sealing joints, and bonding different materials such as glass, aluminum, and concrete. With the growing focus on energy-efficient buildings and sustainable construction practices, SMPs are poised for significant growth in the market.
Get a Free Sample Report with Table of Contents@
Automotive and Aerospace Industries
Silyl modified polymers are also in high demand in the automotive and aerospace sectors due to their excellent mechanical properties, durability, and resistance to extreme temperatures. They are commonly used in vehicle assembly, bonding interior panels, sealing windshields, and in aerospace applications such as sealing aircraft components. SMPs help improve the overall performance, safety, and longevity of vehicles and aircraft, further driving their adoption in these industries.
Electronics and Consumer Goods
SMPs are also gaining popularity in the electronics industry, where they are used for encapsulating and sealing electronic components to protect against moisture, dust, and chemicals. Their excellent electrical insulation properties and thermal stability make them an ideal choice for manufacturing electronic devices and consumer goods.
Key Considerations for SMP Manufacturing Plant Setup
When planning an SMP manufacturing plant, several key factors need to be taken into account. These factors ensure the efficiency, profitability, and sustainability of the operation. Let's explore the key elements involved in setting up the plant.
1. Location Selection
The location of the manufacturing plant plays a critical role in the success of the project. Factors such as proximity to raw material suppliers, transportation networks, labor availability, and government incentives should be considered. The ideal location will help minimize logistics costs and ensure easy access to key markets. Additionally, regulations concerning environmental impact and safety should be carefully reviewed, as manufacturing plants that deal with chemicals and polymers are subject to stringent local and international regulations.
2. Raw Materials and Supply Chain
Silyl-modified polymers are produced using a variety of raw materials, including silane compounds, organic polymers, and other specialty chemicals. Establishing a reliable supply chain for these materials is critical to the production process. Suppliers must be vetted for quality and consistency, and contracts should be negotiated to ensure a steady flow of materials at competitive prices.
Additionally, having a strong network of local or global suppliers can help mitigate risks related to supply chain disruptions. The plant must also be capable of handling large volumes of raw materials and managing inventory efficiently to prevent production delays.
3. Technological Infrastructure
An SMP manufacturing plant requires advanced equipment to handle the polymerization process, including reactors, mixers, and extruders. The technology employed must meet industry standards to ensure the quality and consistency of the final product. Automation can also be integrated to optimize the manufacturing process, improve efficiency, and reduce human error.
The production process itself typically involves the mixing of silane-modified resins and other components to create a uniform blend. The mixture then undergoes polymerization, a chemical reaction that forms the desired polymer structure. The process may vary slightly depending on the type of SMP being produced and the intended application.
4. Production Capacity and Scalability
Establishing the production capacity is one of the key elements of the project plan. The size of the manufacturing facility will depend on the scale of production required to meet market demand. It is important to balance production capabilities with projected sales volumes to avoid over- or under-production.
Scalability is also a consideration in the early stages of planning. The plant should be designed with future expansion in mind, enabling it to scale production capacity without significant capital investment or operational disruptions. Modular production lines or additional equipment can be added over time to accommodate increasing demand.
5. Environmental and Safety Compliance
Given that SMP manufacturing involves the use of chemicals and high-energy processes, environmental and safety considerations are paramount. The plant must adhere to local and international environmental regulations to minimize its carbon footprint, waste generation, and energy consumption.
Advanced filtration and waste management systems should be incorporated to handle emissions, fumes, and chemical byproducts. Furthermore, safety protocols and systems should be in place to protect workers from exposure to hazardous substances. Regular safety training and certification should be mandatory for all employees.
Financial Aspects of the SMP Manufacturing Plant
The financial feasibility of the SMP manufacturing plant is another crucial component of the project report. Proper financial planning ensures the plant's long-term profitability and helps secure funding from investors or financial institutions.
1. Capital Investment
The initial capital investment for an SMP manufacturing plant is typically significant, as it involves purchasing land, constructing the facility, acquiring machinery, and setting up the supply chain. Additionally, the cost of raw materials and hiring skilled labor should be factored into the budget.
Funding sources could include venture capital, bank loans, or government subsidies, especially if the plant is established in an area where environmental sustainability is a priority. A solid business plan that highlights the projected ROI (Return on Investment) and payback period will be essential for attracting investors.
2. Operational Costs
Operational costs for the plant will include expenses such as labor, utilities (e.g., water, electricity), raw material procurement, and maintenance of machinery. The manufacturing process itself should be optimized to reduce wastage and ensure maximum efficiency in resource utilization. Ongoing research and development (R&D) costs will also be necessary to improve the quality of the final product and stay ahead of competitors.
3. Revenue Projections
Revenue projections are based on several factors, including the production capacity, market prices, and expected demand for SMPs. Pricing strategies should consider the cost of production, competition, and the perceived value of the product in the market. SMP manufacturers can also diversify their product portfolio by offering various grades or formulations of SMPs tailored for different industries.
An accurate financial model should forecast revenues, expenses, and profits over the next 5 to 10 years, accounting for market fluctuations, industry trends, and potential changes in regulations.
Project Timeline and Implementation
The timeline for setting up an SMP manufacturing plant can vary based on the size and complexity of the project. The project typically unfolds in several stages:
- Feasibility Study and Market Research: Conducting a thorough market study and feasibility analysis to gauge demand and assess the competition.
- Site Selection and Permits: Securing the plant location and obtaining the necessary permits and licenses.
- Design and Construction: Designing the facility layout and building the plant infrastructure.
- Equipment Installation: Installing machinery and setting up the production lines.
- Staff Recruitment and Training: Hiring skilled personnel and providing them with the necessary training to operate the plant efficiently.
- Trial Runs and Quality Control: Conducting initial trials to fine-tune the production process and ensure the product meets quality standards.
- Full-Scale Production: Once the plant is fully operational, production can begin at full scale.
Company Name: Claight Corporation
Contact Person: Peter Fernandas, Corporate Sales Specialist — U.S.A.
Email: sales@expertmarketresearch.com
Toll Free Number: +1–415–325–5166 | +44–702–402–5790
Address: 30 North Gould Street, Sheridan, WY 82801, USA
Website: www.expertmarketresearch.com
Aus Site: https://www.expertmarketresearch.com.au
- Art
- Causes
- Crafts
- Dance
- Drinks
- Film
- Fitness
- Food
- Jeux
- Gardening
- Health
- Domicile
- Literature
- Music
- Networking
- Autre
- Party
- Religion
- Shopping
- Sports
- Theater
- Wellness
- IT, Cloud, Software and Technology